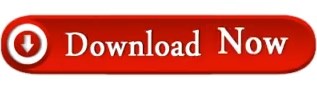

I like to edit STL data in Materialise Magics, or Design X. And select Environments and select stress analysis you see Icon mesh View. If your STL mesh is terrible to begin with, the resulting CAD model is also going to have defects. You must be a three-dimensional model of a part of its Solid material draw from the selection properties.then save the file. Answered on 20 Dec, 2014 04:45 AM Hi there. You can also change the value with the mesh_enhance_gradation in the Flag Manager. How can I get mesh enabler for student access Please. When simulating external aerodynamics with the SST k-omega turbulence model, a low value of y+ is essential for accurate flow prediction. This is an effective way to reduce the element thickness near the wall and the value of Turbulence y+. When the Number of layers is greater than 5, you should change the Layer gradation value from Auto to a value. When this option is enabled, any Actor with Onion Skinning defined for it displays as designated in the 3D viewport (the default state). Use this setting to improve the accuracy of heat flux at the wall as well as for the SST k-omega turbulence model. This option should be thought of as a global enabler only, where the actual display of the silhouette itself is determined by the options of the items Display properties. Gradation allows the layers nearest the wall to be smaller than those closest to the neighboring unstructured elements. As the number of enhancement layers increases, the layer thickness often has a tendency to become uniform. Use Layer gradation to control the rate of growth of the enhancement layers. Reduce this factor for thinner layers and reduced total thickness. The layer height is determined by multiplying this factor by the local isotropic length scale for that surface. Rotating-region analyses, you can improve stability by reducing the number of layers to 1.Ĭontrols the layer thickness. In the latter case, meshes that have been enhanced have been shown to be significantly less disruptive than non-enhanced meshes to the flow near the walls, resulting in improved flow uniformity throughout the channel. Examples include flows in which the turbulence is very sensitive to the flow near the walls and within long, narrow channels.

Layer uniformity is important for accuracy in certain analyses. Gradual transitioning between surfaces ensures gradual variations in element height throughout the model. Element layer height across each surface is uniform, and is based on the smallest length scale on a surface. Diagnostic algorithms detect and avoid element clashes in small gaps automatically. Mesh Enhancement creates layers before the 3D mesh is constructed. Mesh Enhancement ensures adequate mesh across small gaps, which can be very difficult manually. It augments the original mesh to produce a smooth distribution along all walls, which is critical for accurate flow and temperature prediction. Mesh Enhancement adds element layers along all fluid-wall and fluid-solid interfaces.
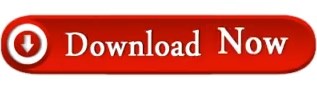